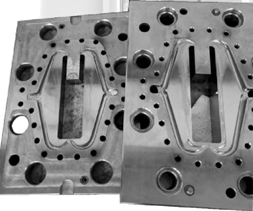
Description
CO extrusion tooling utilizes specialized dies to extrude multiple materials simultaneously into a single product. This advanced manufacturing process enables the creation of complex profiles with varying layers, each offering unique properties. Widely used in industries such as automotive and packaging, CO extrusion tooling delivers products with enhanced performance, aesthetics, and functionality.
Features and Applications of CO Extrusion Tooling
Key Features
- Precision Engineering: Ensures exact layering and material distribution for consistent quality.
- Versatility: Accommodates a wide range of materials and complex profile designs.
- Efficiency: Optimizes production speed while maintaining high-quality outputs.
- Enhanced Product Properties: Combines materials with different characteristics into a unified product.
Applications
CO extrusion tooling supports a variety of industries and products, including:
- Automotive Components: Multi-layered trims, seals, and interior panels.
- Packaging Solutions: Films, containers, and protective layers with superior durability and barrier properties.
- Construction Materials: Multi-layer profiles for windows, doors, and weatherproofing applications.
- Consumer Goods: Durable and aesthetic profiles for appliances and household items.
Types:
COEX Tooling Components
- Screws and Barrels: Melt and mix the raw materials for uniform consistency.
- Manifolds: Distribute materials evenly into the die for layering.
- Dies: Shape the combined materials into the desired profile, ensuring accuracy and quality.
Specialized Dies
Custom dies designed to accommodate specific product requirements, such as thickness, material compatibility, and profile complexity.
Benefits of CO-Extrusion Tooling
- Material Efficiency: Combines properties of multiple materials, reducing waste.
- Improved Performance: Enhances product functionality by integrating unique layers.
- Cost Savings: Reduces the need for secondary processing or assembly.
- Customizability: Enables tailored designs for specific industry needs.
Process Overview
- Material Feeding: Feeding multiple raw materials into separate extruders.
- Melting and Mixing: Heating and blending the materials in screws and barrels.
- Layer Distribution: Manifolds ensure even layering before extrusion.
- Shaping: Specialized dies shape the material into the desired profile.
- Cooling and Solidification: Ensures dimensional stability and layer adhesion.
Applications
Related products
-
Extrusion toolings and moulds
EXTERNAL WALL CLADDING AND CEILING PANEL TOOLING
-
Extrusion toolings and moulds
WPC Tooling
-
Extrusion toolings and moulds
Profile Tooling
-
Extrusion toolings and moulds
Building Material Tooling